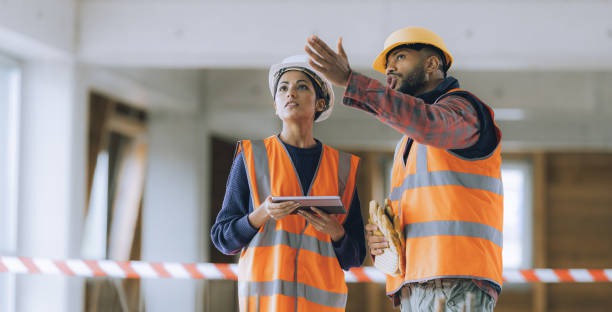
Expert Tips: Key Essentials for Building a Refrigerated Warehouse
Constructing a refrigerated warehouse can seem daunting. However, with a little bit of knowledge and some expert guidance, you’ll find the process to be manageable and even enjoyable. The unique challenges and requirements of such projects make it crucial to approach them with careful planning.
1. The Importance of Site Selection
Let’s start with the basics—choosing the right location. Your site needs to meet several key criteria:
-
Accessibility: Make sure it’s easily accessible for trucks and other logistics services.
-
Utilities: Check that utilities like electricity and water are readily available.
-
Environmental Conditions: Consider any local climate factors that may impact the long-term performance of your warehouse.
Each of these elements can directly affect the efficiency and cost-effectiveness of your project.
2. Specialized Design Considerations
Designing a refrigerated warehouse isn’t just about keeping the heat out. Instead, it involves a multitude of factors:
-
Temperature Zones: Depending on the kind of goods you’ll store, you may need multiple temperature zones under one roof.
-
Insulation: Adequate insulation helps maintain the internal climate more efficiently.
-
Ventilation: While minimizing warm air intrusion, you also need to ensure proper ventilation for safety reasons.
These specialized design features ensure optimal storage conditions, maintaining product quality and minimizing energy costs. To learn more about these features, click here.
3. Materials Matter
Choosing the right materials is essential for any construction project, but it is especially important for refrigerated warehouses. For example, walls and flooring must not only help maintain low temperatures but also withstand the stresses of heavy traffic and storage.
Concrete Takes the Floor
Concrete is a popular choice for flooring due to its durability. However, certain coatings or treatments must be added to make it suitable for low temperatures. Concrete inevitably expands and contracts, and without proper treatment, you’ll run into issues like cracking or moisture penetration.
4. Understanding Mechanical Systems
Building a refrigerated warehouse involves not only constructing a cold room but also integrating complex mechanical systems, which are essential for maintaining temperature stability.
The Role of Refrigeration Equipment
Modern refrigeration systems often include components like:
-
Compressors
-
Condensers
-
Evaporators
Each has a role in the cooling process and is crucial for maintaining the efficiency of your refrigerated warehouse.
Energy Efficiency Is Key
Let’s talk about energy efficiency. The energy needs of a refrigerated warehouse can be significant, but there are ways to keep costs down:
-
Energy-efficient equipment like LED lighting and high-efficiency compressors
-
Effective insulation and sealing techniques to prevent air leakages
-
Cool roofs or garden roofs that reflect more sunlight and absorb less heat
Such strategies help reduce operational costs while benefiting the environment.
5. Focusing on Safety Measures
Safety is a paramount concern when constructing a refrigerated warehouse. It’s crucial to integrate safety measures into both the design and construction processes.
Focus on Worker Safety
A few of the key safety features you should consider include:
-
Adequate signage to alert workers to hazards
-
Proper lighting to enhance visibility in all areas, including emergency exits
-
Anti-slip flooring to prevent accidents
Safety features not only protect your employees but also create a more productive and efficient working environment.
Making It Seismic-Ready
Depending on your geographical area, you may need to implement seismic design measures. These measures involve reinforcing the warehouse’s structural integrity to withstand earthquakes.
6. Consulting the Experts
Constructing a refrigerated warehouse is a specialized task that benefits from expert oversight. Consulting with professionals at different stages ensures that your project complies with all applicable codes and standards. Plus, they bring valuable experience to help troubleshoot issues before they become costly problems.
Many businesses opt for professional commercial construction services to handle such complex projects. These services can manage everything from design to logistics and compliance, allowing you to focus on other crucial aspects of your business.
7. Infusing Technology
Technology makes a world of difference when achieving precision in your refrigerated warehouse construction project.
Smart Building Solutions
Modern technologies are now part of the construction landscape, offering incredible efficiencies:
-
Use of IoT devices to monitor and control the temperature.
-
Advanced data analytics for predictive maintenance of refrigeration equipment.
-
Smart lighting systems that adjust to occupancy and daylight availability.
By integrating these tech solutions, you can achieve significant savings in both time and cost.
8. Ensuring Longevity and Performance
After construction, the warehouse should be able to sustain its operations efficiently for years to come. Maintenance plays a pivotal role here.
Regular Maintenance Checks
Scheduled maintenance checks go a long way in keeping the facility operational:
-
Check seals and doorways for leaks.
-
Assess refrigeration units for wear and tear.
-
Ensure ventilation systems are free of obstructions.
Such practices help maintain the efficiency and longevity of your facility.
Utilizing Refrigerated Warehouse Construction Services
There are companies specializing in this type of construction who know exactly what needs to be done. These excellent refrigerated warehouse construction services ensure the warehouse will meet all operational and safety requirements while being efficient and durable.
Adaptable Design
Incorporate design features that allow for future upgrades or changes in technology. This can include modular wall systems or flexible refrigeration setups that are easy to adjust as your needs evolve.
Concluding Thoughts
Building a refrigerated warehouse isn’t simple, but it is incredibly rewarding when done right. By focusing on each stage—site selection, design, construction, and maintenance—you set the groundwork for a facility that will serve your needs for years to come. Pay attention to every detail, consult experts when needed, and don’t shy away from using modern technology to your advantage. Your next build will not only be efficient but also a model of success for years to come.